Manufacturing companies need to ensure their equipment runs optimally in order to remain competitive, but repairs and maintenance can be expensive and time-consuming. Fortunately, many of these businesses now have access to a cost-effective solution: remote expert maintenance.
By leveraging the latest technologies to connect with experienced technicians from around the globe, manufacturing companies are able to quickly and efficiently diagnose, troubleshoot, and repair their equipment with minimal disruption. Remote experts (‘experts’ are subject-matter specialists who have expertise on a specific piece(s) of equipment) offer an efficient solution for manufacturing companies looking to overcome labor shortages and quickly repair equipment remotely.
The labor shortage in the manufacturing industry
The manufacturing industry has long been a cornerstone of the global economy, creating countless jobs, and producing essential goods that we use on a daily basis. However, the industry is facing a major challenge: a shortage of skilled labor. This labor shortage has become especially severe in recent years, and it is estimated that the U.S. manufacturing sector will lose 3.5 million skilled workers to retirement in the next decade. If this continues, by 2030, there could be 2.1 manufacturing jobs available with no one to fill them leading to a potential cost of 1 trillion dollars.
The labor shortage in the manufacturing industry is a result of several factors, including the aging workforce and the lack of skilled workers. In addition, the negative perception associated with working in the manufacturing industry has made it difficult for manufacturers to attract and retain talent. As a result, the industry is struggling to find workers to fill the increasing number of job vacancies.
The challenges faced by manufacturers due to the labor shortage
The labor shortage is not just a problem for manufacturers; it has also created a ripple effect throughout the economy. Manufacturers are facing a significant challenge in meeting production demands, which is leading to delayed shipments, loss of revenue, and customer dissatisfaction. Moreover, the shortage of skilled workers is impeding the innovation and advancement of the industry, which may have long-term impacts on its growth and sustainability.
According to a survey through the National Association of Manufacturers, the #1 business challenge facing 75% of manufacturing leaders in the U.S. is attracting and retaining quality workers. At the beginning of the pandemic, the U.S. lost 1.4 million manufacturing jobs, and while two-thirds of those came back, it still left a hole in the manufacturing workforce.
Manufacturers should consider using remote experts for equipment repair
Manufacturing has been greatly affected by the labor shortage, which can cause equipment downtime and production delays. However, with technology advancements, manufacturers now have access to remote experts, who can help address these issues.
Who are remote experts?
Remote experts are subject-matter experts who specialize in the maintenance and repair of machinery. They connect virtually with an employee of a business and provide valuable support services such as troubleshooting, repair consultations, assistance with diagnostics, parts replacement, and programming. Remote experts not only offer a cost-effective solution to equipment maintenance but also help reduce downtime due to their quick response times.
What is remote expert technology & how is it better than a phone or video call?
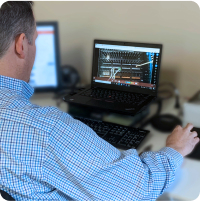
Remote expert technology is specialized software that enables a manufacturer’s staff or equipment technician to connect with an off-site expert to repair equipment.
One vehicle for this technology is smartglasses. The technician wears the smartglasses and the expert, who is working from a remote location, is logged into the software’s dashboard and can see everything the technician sees via the camera. The technician can work hands free and move around the equipment and the facility, while the expert guides them through the repairs. It’s as if the expert was standing right there with the technician. This approach decreases the need to travel in-person, fixing the problem in days, not weeks.
Many smartglasses companies and software providers have seen the practical use for the smartglasses in the industry and have adapted their hardware and software for the environment. With improved safety measures and sturdy yet light designs, technicians don’t have to worry about smartglasses inhibiting their safety or getting damaged while in use. And while most remote calling softwares work on smartglasses like Microsoft Teams and Zoom, they weren’t created with industry in mind. Many remote expert softwares enable the expert to share annotations of what they see to the technician on the other end, highlighting, for example, a missing bolt a technician may be overlooking. In addition, experts have the ability to share schematics, manuals, and PDFs all in someone’s line of sight as they work. This combination of highly customized software and hardware for the industry creates a direct and easy way of communicating that effectively saves time, money, and resources.
Assisted reality and remote experts can help manufacturers address the labor shortage
Remote experts can help manufacturers address the labor shortage by providing efficient and accurate repair services. This technology eliminates the need for on-site field service technicians, which allows manufacturers to access a larger pool of expertise at a lower cost than hiring full-time staff. Remote experts are also available 24/7, making them more reliable than traditional technicians who may be limited to business hours.
How equipment repair issues can be resolved remotely
Equipment repair issues can range from simple issues, such as replacing a part, to more complex problems, such as diagnosing a mechanical malfunction. Remote experts can help address these issues by providing real-time visual support and step-by-step instructions, which allows manufacturers to reduce the costs of travel for specialists to address the problem on-site with real-time support. For instance, a manufacturer in the packaging industry might encounter a problem with their shrink wrapping equipment in one of their facilities, and a remote expert in another state, or even another country, could help diagnose and fix the issue by virtually looking over the technician’s shoulder.
Other ways manufacturers can benefit from using remote help include using remote experts to improve their quality control measures. Additionally, remote experts can help their peers on the manufacturing floor with troubleshooting technical issues and identifying areas of improvement within the manufacturing process.
Case study

Bühler, a global supply chain company, utilized our Assisted Reality platform and saw a 35% improvement in efficiency, saving them $30k a day. They also experienced a 55% reduction in travel expenses and a 22% uptick in customer support satisfaction.
Cutting down costs with remote experts
Manufacturing companies often depend on efficient and effective machinery to keep production running smoothly. But when equipment malfunctions, these companies are left with a difficult choice: spend time and money bringing in an expert technician for repairs, or attempt DIY repairs that may not be successful. Fortunately, there is now a third option, using remote experts for equipment repair.
How remote experts can help manufacturers avoid costly downtime
First and foremost, remote experts can help manufacturers avoid costly production downtime. When equipment fails, it can result in a significant loss of production, which ultimately leads to a decline in revenue. A remote expert can identify the problem quickly and provide real-time guidance to get the equipment running again, minimizing downtime and the associated costs.
Additionally, remote experts offer up their expertise to younger and less experienced technicians, enabling them to learn from more experienced professionals.
More cost benefits of using remote experts
Remote experts allow you to save costs on travel expenses. In traditional repair methods, when a machine breaks down, manufacturers either have to wait for a technician to arrive at their plant or, depending on the equipment, send the machine to a repair facility. With remote expert solutions, manufacturing companies can contact experts virtually via the NewForge Knowledge Place platform while using assisted reality to receive real-time guidance to repair the issue without anyone needing to travel. Therefore, manufacturers can save costs in travel expenses such as transportation and accommodation. It’s a win-win situation where both the manufacturer and expert save time and expenses.
Furthermore, remote experts provide better cost predictability. Traditional repair methods are costly due to unpredictable expenses, such as delays in travel, out-of-hours work fees, and unexpected maintenance expenses. With remote expert solutions, manufacturers can expect fixed costs with no hidden fees other than subscription or service fees. As a result, the manufacturer can plan their budget efficiently and allocate funds to other essential areas of their business.
Remote expert services versus traditional repair methods
In terms of cost comparison, remote expert solutions are more cost effective than traditional repair methods. Manufacturers only have to pay for remote expert technicians when they need them, making it more affordable in the long run.
The future of remote expert technology in manufacturing
The potential of remote expert technology to revolutionize the manufacturing industry is truly an exciting prospect. Augmented reality (AR) technology is predicted to become more commonplace among manufacturing companies. It allows experts to “see” and diagnose problems with machines in a virtual environment, providing them with additional insight into the issue.
From increased efficiency and productivity to cost savings and improved customer experiences, remote expert technology in manufacturing is certainly something to keep an eye on. Stay tuned for additional Knowledge Place features that will greatly enhance the future of work!
Article Comments
pocket option
May 7, 2024 1:25 pmIt’s difficult to find educated people for this subject, but
you sound like you know what you’re talking about!
Thanks